Seit zwei Jahrzehnten tüfteln Spezialisten an einem neuen Verfahren, mit dem Chlor mit weniger Energieaufwand hergestellt wird. Mit Erfolg: Gerade wurde in Tarragona die erste Covestro-Großanlage angefahren.
„Highlight meiner Karriere“So sorgen Covestros Leverkusener Ingenieure für eine sparsamere Chlorfabrik
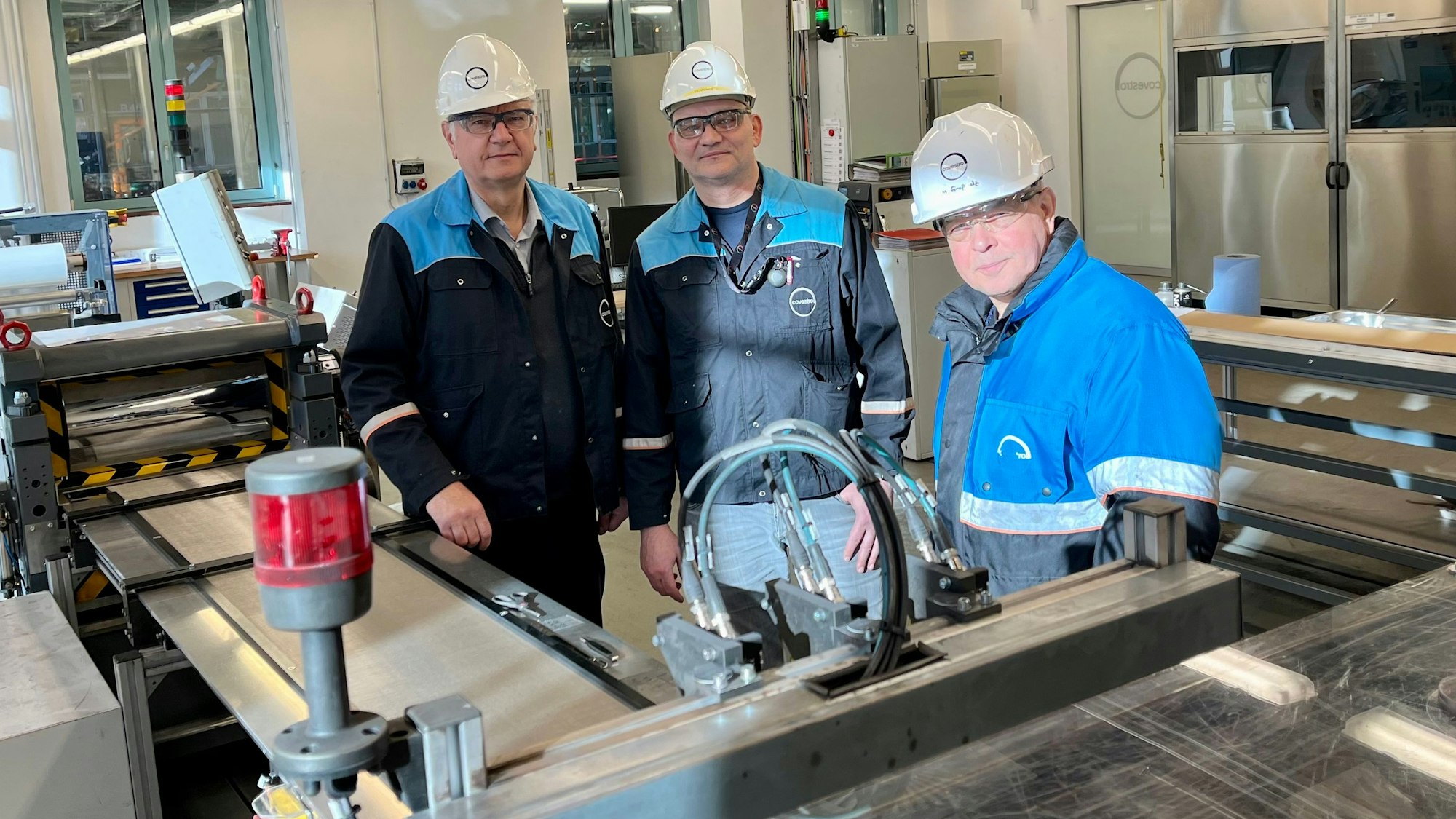
Andreas Bulan, Roberto Warthe und Michael Großholz (v. l.) an der selbst konstruierten Anlage, auf der Covestro Sauerstoff-Verzehrkathoden baut.
Copyright: Thomas Käding
Andreas Bulan macht es in einem Satz klar: „Chlor ist unser Motor.“ Als er vor 41 Jahren angefangen hat, hieß die Firma noch Bayer und der Chemie-Ingenieur hat wohl nicht gedacht, dass er sein halbes Berufsleben der Sauerstoff-Verzehrkathode widmen würde. Aber die Herstellung von Chlor und Natronlauge ist für seine Industrie ein dermaßen zentraler Prozess, dass er Tüftelei mit offenem Ende rechtfertigt.
Wegen der Massen an Chlor, die unter dem Bayer-Kreuz verbraucht werden. Aber auch wegen der unfassbaren Mengen an Strom, die man dafür benötigt: Die Leverkusener Chlorfabrik verbraucht – über den Daumen – so viel wie halb Köln.
Chlor und Natronlauge müssen verfügbar sein wie Strom aus der Steckdose
Da ist ein Verfahren, mit dem man Chlor und Natronlauge herstellt und dabei rund ein Viertel weniger Energie verbraucht, natürlich eine Verheißung. Wenn’s denn nur so einfach wäre: Die Elektrolyse mit Hilfe der Sauerstoff-Verzehrkathode (SVK) ist „eine schwierige Technologie“, fasst Bulan am Dienstag gut zwei Dekaden Entwicklung zusammen.
Alles zum Thema Leverkusen Chempark
- Quartalszahlen Wie Wirtz und Frimpong Bayers Bilanz verbessern
- Finanzkrise Leverkusen nimmt noch weniger Gewerbesteuern ein als geplant
- Zahlen der Kämmerei Leverkusens Finanzkatastrophe wurde im Chempark ausgelöst
- Kläranlage Wieder Ärger um Rückstände im Rhein bei Leverkusen
- Warn-App löste aus Feuerwehr gibt Entwarnung nach „Schadensereignis“ im Chempark Dormagen
- Ukraine Zwischen Bayerwerk und Kachowka-See: Kunstprojekt verbindet Nikopol und Leverkusen
- Chempark in Leverkusen Größere Menge Titandioxid in Rhein gelangt
In dieser Zeit wurde aus der Theorie ein praktisches Verfahren gemacht, das am Ende auch den Nageltest großindustrieller Produktion bestehen kann. Chlor und Natronlauge „müssen verfügbar sein wie Strom aus der Steckdose“, beschreibt der Ingenieur die Anforderung. Das heißt: Ausfälle sind nicht vorgesehen.
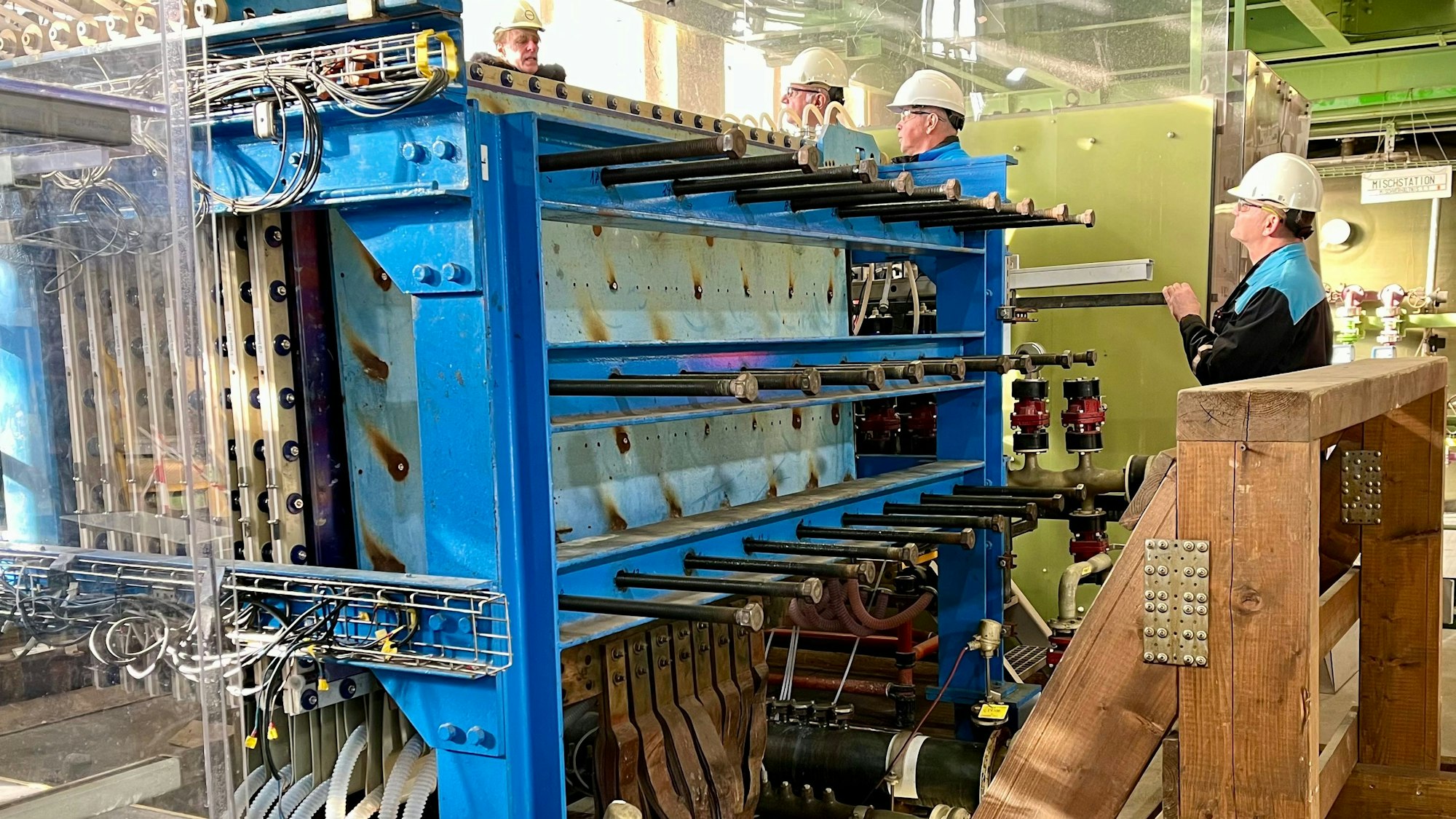
In einem kleinen Elektrolyseur wurde das neue Verfahren getestet.
Copyright: Thomas Käding
Gerade ist Bulan mit Michael Großholz und einigen anderen Kollegen aus Tarragona an der spanischen Costa Brava zurückgekommen. Die drei letzten Wochen, bevor im Covestro-Werk dort am Montag der Schalter umgelegt wurde für die erste SVK-Chlorfabrik der Welt, haben die Leverkusener noch Hand angelegt, dem rund 50 Personen starken Team, das die „World-Scale-Anlage“ dort fahren wird, ein paar Tipps gegeben zu den Besonderheiten des Verfahrens.
Die Technik der Brennstoffzelle
Die haben sie von den ersten, handgemachten Sauerstoff-Verzehrkathoden über den Versuchs-Elektrolyseur in Uerdingen in viel Kleinarbeit und mit Hilfe der Kollegen von Thyssen-Krupp Punkt für Punkt herausgefunden. Es seien „viele, viele Hürden“ zu überwinden gewesen, bis das Verfahren tatsächlich verlässlich einsatzfähig war, bilanziert Bulan.
Denn die Brennstoffzellen-Technik, die dem SVK-Verfahren im Prinzip zugrunde liegt, helfe leider nur zum Teil bei der Entwicklung einer Chlorfabrik. Hilfreich sei aber, dass ein Elektrolyseur skalierbar sei. Dass also, anders ausgedrückt, was in einer Zelle funktioniert, auch in zehn Einheiten klappt.
Vorausgesetzt, die Bestandteile werden in gleichbleibender Qualität hergestellt. Das sei gar nicht so einfach gewesen, erinnert sich Roberto Warthe beim Gang durch die Hallen, in denen seit der Jahrtausendwende an dem neuen Verfahren gearbeitet wird: Der Industriemeister sammelt seit 2005 Erfahrungen in der Herstellung von Sauerstoff-Verzehrkathoden. Und weiß, dass es durchaus nicht so ist, dass eine maschinelle Fertigung der Handarbeit überlegen ist.
Der Schritt von der SVK-„Manufaktur“ zur kleinen Fertigungsstraße in der Halle nebenan sei ziemlich kompliziert gewesen. Rund eineinhalb Jahre habe es allein gedauert, die Herstellungsschritte auf die Maschinen zu übersetzen. „Zum Glück haben wir in Deutschland noch die Hersteller für Präzisionsteile“, sekundiert Andreas Bulan und deutet auf die Walzen, unter denen das Metallgewebe nach seiner Beschichtung herläuft.
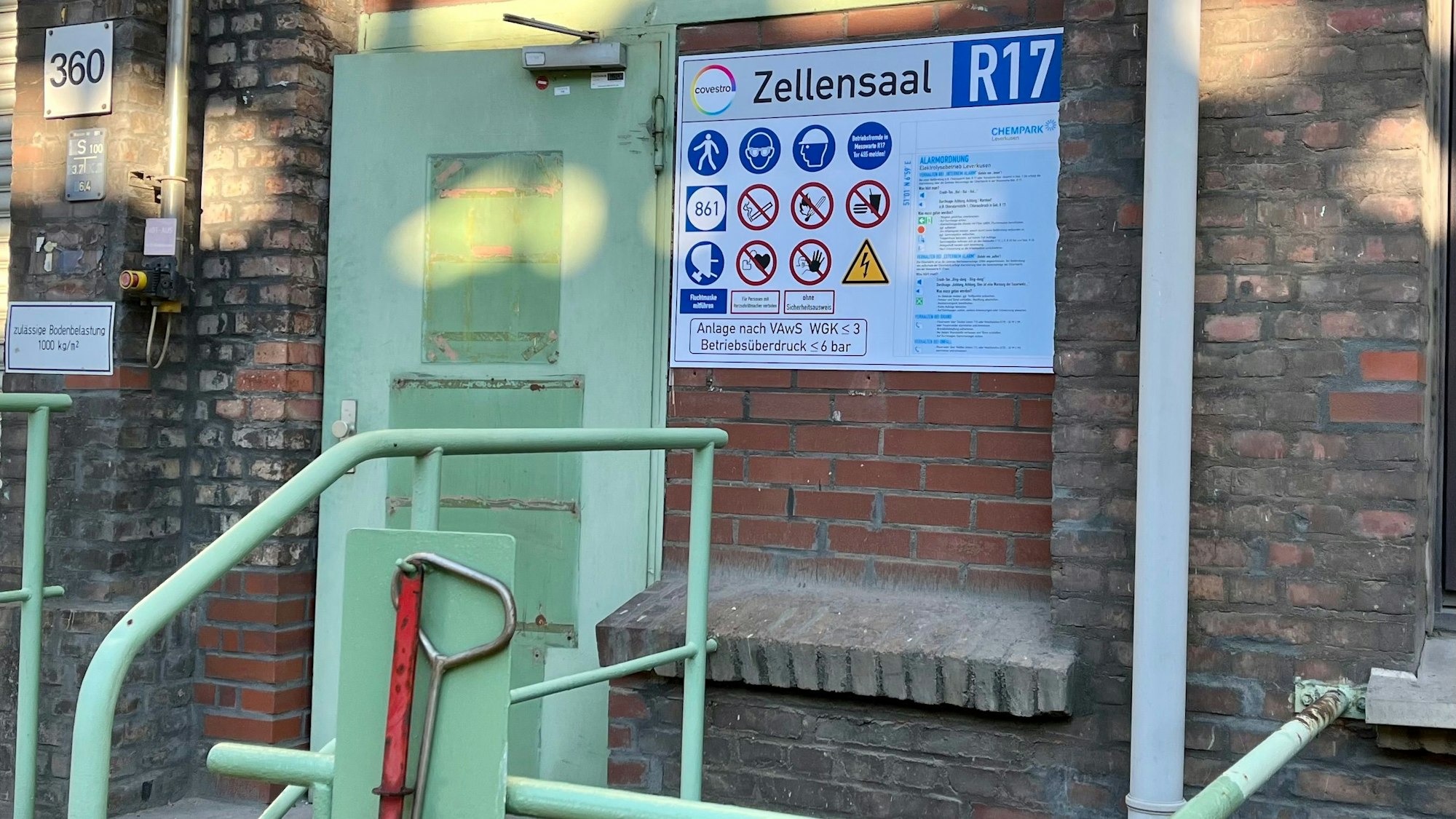
Eingang zum Herzstück der Chlorfabrik: dem Zellensaal
Copyright: Thomas Käding
Die rund zweieinhalb Meter langen und geschätzt 40 Zentimeter breiten Platten werden nach ihrer Herstellung sorgfältig verpackt und verschweißt. Danach gehen sie nach Tarragona, um den Betrieb der neuen Chlorfabrik sicherzustellen. Allzu schnell verschleißen sollten sie freilich nicht. Die Spezialisten bei Covestro rechnen mit einer Lebensdauer von fünf, wenn es gut läuft sogar bis zu acht Jahren.
Ob sie irgendwann auch für die Chlorfabrik nebenan Sauerstoff-Verzehrkathoden herstellen, ist offen. Der Strom-Einsparung von rund einem Viertel, weil bei diesem Elektrolyse-Verfahren einfach weniger Energie an der Kathode anliegen muss, steht entgegen, dass kein Wasserstoff anfällt. Der wird aber im Chempark gebraucht.
Fragt sich nur, ob es nicht effizientere Verfahren gibt, Wasserstoff zu gewinnen. Aber das ist für Covestros Elektrolyse-Spezialisten eine ganz andere Frage. Für Andreas Bulan ist indes sicher: Die Inbetriebnahme der ersten „World-Scale-Anlage“ in Tarragona „ist das Highlight meiner Karriere“.
Hergebrachtes Membranverfahren verbraucht viel Strom
In Leverkusen werden die Basischemikalien Chlor, Natronlauge – und Wasserstoff als Abfallprodukt – noch nach dem Membranverfahren produziert. Der Prozess wurde zwar in den vergangenen drei Jahrzehnten immer weiter optimiert, sodass der Stromverbrauch um rund zehn Prozent gesenkt werden konnte, benötigt aber systembedingt mehr Energie.
In Tarragona hat Covestro bisher Chlor und Natronlauge zugekauft. Die Chlorfabrik dort wurde bis zu ihrer Schließung nach dem noch älteren Amalgam-Verfahren betrieben, das in Europa aus Umweltschutzgründen nicht mehr erlaubt ist: Dabei fallen große Mengen Quecksilber an.
Es benötigt außerdem noch mehr Energie. Covestros Vorstandschef Markus Steilemann beziffert die CO₂-Einsparung allein bei der Chlor-Herstellung nach dem SVK-Verfahren auf bis zu 22.000 Tonnen pro Jahr.